Petit support pour
servomoteur d'aiguillage
Depuis le temps que je fabrique des décodeurs pour servomoteurs,
c'était fatal, j'allai devoir inventer un support.
Il en existe bien dans le commerce, notamment chez PECO, mais le
support est à monter SUR la table
à coté de l'aiguille. Et vu le prix pratiqué
, ça va pas le
faire ! 
Eh puis voilà... ça n'a pas traîné, l'association (AGAT) où
je sévis en a eu besoin. Je me suis donc lançé dans la concception. 
Voir la mise à jour du 22/11/2016
1/ Toute
conception commence par un cahier des charges :
C'est mieux de savoir où on va...alors on fixe de suite les objectifs.
- Une chose est sûre : Le servomoteur sera SOUS la table ou ne sera pas du tout !
- Au niveau de l'effort de maintien on a un impératif à respecter car les aiguillages du nouveau
réseau sont des "tillig"...

Tous ceux qui connaissent ces "Tillig" savent que les aiguilles n'ont
pas de ressort de maintien
de fin de course (zut!), et les lames
souples sont relativement raides
(re-zut!) puisqu'elles ne
comportent pas d'articulation (ah çà c'est glop !
). Donc, exit les
bobines PECO et compagnie.
- En plus, ce sont des aiguillages à ceur polarisé. La polarité du coeur
d'aiguille doit changer en fonction de la position du servomoteur. Il faut donc intégrer un switch.

En résumé ca fait 4 critères : 
- Il faut utiliser un moteur
capable de maintenir un effort élevé en bout de course
- Il faut avoir un mouvement lent (NOOOON! pas les tortoise !!! t'as
vu le prix????? )
- Il faut être réglable.
- Il faut pouvoir agir sur un interrupteur inverseur.
2/ Solutions
retenues :
Concernant la motorisation, le servomoteur s'imposait, j'ai choisi des microservos "towerPro"
comme celui-ci, surtout pour leur PRIX défiant toute concurence.
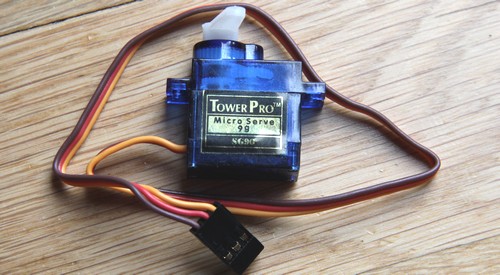
Ensuite, il fallait bien maintenir le servomoteur en place sous le
réseau et répondre aux 4 critères ci-dessus. Une pièce intermédiaire
s'imposait.
Bon, je passe sur les différents éssais plus ou moins réussis, passons
directement à ce qui marche :
Un "joli"
petit support avec des formes compliquées comme tout. Il faudra
que je revoie le design...

- La forme centrale et le plan
supérieur reçoivent le servomoteur,
- Une rainure de 25mm en dessous permet le guidage de la tige sans
mouvement parasite
- Un creux sur le coté avec 2 tétons permer le positionnement du
microswitch
- Deux rainures oblongues permettent de placer une vis de chaque coté
avec un petit réglage.
Ce dernier point n'est pas super à l'usage, il faut que je vevoie
ça.
Je l'ai réalisé avec le logiciel SolidWorks, ce qui m'a permis
d'intégrer toutes les formes nécessaires et vérifier le bon
fonctionnement.
- J'ai aussi modélisé la tige de commande : Ce n'est pas
l'élément le plus compliqué mais il demande une élasticité
particulière. Trop "mou" il serait incapable de transmettre le
mouvement, et trop "raide" il exercerait un effort trop élevé sur
l'aiguillage.
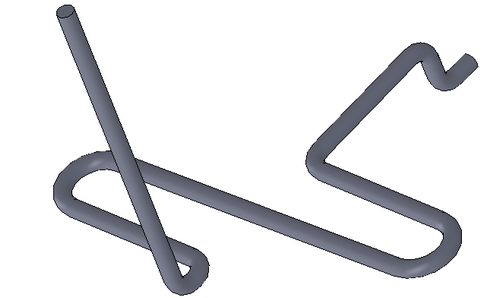
- Les grands zig-zag servent à
faire "ressort".
- Le petit zig-zag du bout permet de rentrer et d'être maintenu dans le
levier de commande du servomoteur.
3/
Fontionnement :
La rotation du servomoteur "pousse" ou "tire" la tige de façon à
provoquer la translation de la traverse mobile de l'aiguille.
Lorsque l'aiguille arrive en butée, le ressort de la tige se déforme
pour "absorber la différence de course entre l'aiguillage et le
servomoteur.
La vidéo vaut bien mieux que de longues explications :
Servomoteur d'aiguillage support sous table
par StephaneMONTARGIS
4/ Réalisation :
Il y a donc deux pièces majeures à réaliser :
- Le support
- La tige ressort
Le
support :
Les formes n'étant par réalisables par usinage classique, j'ai utilisé
le prototypage rapide.
La prototypeuse utilisée fonctionne sur le principe du laminage par
couches :

Chaque couche successive est découpée puis collée à la couche suivante.

Après avoir débarassé le modèle de tout le support inutile (assez long
quand-même), On obtient ça :

Merci à Florian pour les photos.
La tige réglable :
Vachement plus simple !
Le matériau de base a été trouvé dans une gaine en plastique ! C'est le
petit câble en acier qui sert à tirer les fils dans la gaine.

Coût nul ! j'adore !
Quelques coups de pince bien placés et adaptés à la configuration
voulue, et le tour est joué !
TADAAAAAA! en moins de 30 secondes !
5/ Mise en place
La mise en place est assez facile. Il suffit d'introduire la tige dans
le trou de la traverse et de régler la position idéale. Le maintien se
fait à l'aide de 2 petites vis.


(merci à Florian pour les photos)
Le raccordement électrique est des plus simple.:
- Le commun du switch est raccordé au coeur (fil blanc),
- Le contact NO (normalement ouvert) est à raccorder à un rail de l'aiguillage (Le fil rouge)
- Le contact NF (normalement fermé) est à racorder au second rail, de
polarité opposée (le fil grisGris).
Le réglage est assez facile :
- On place "grosso-modo" le support pour être en butée d'un coté.
- On règle de façon fine chaque butée en utilisant les CV du décodeur de servomoteur
Et voilà !
Ceci dit, ce système fonctionne sur n'importe quelle aiguille
comportant un petit trou sur la traverse mobile. Ca peut être une bonne
solution si, par hasard, votre bobine PECO n'a pas assez de punch pour
manoeuvrer une aiguille.
6/
Un nouveau modèle !
J'ai conçu et mis en place pour mon club un nouveau modèle de commande. Il utilise toujours les servomoteurs.
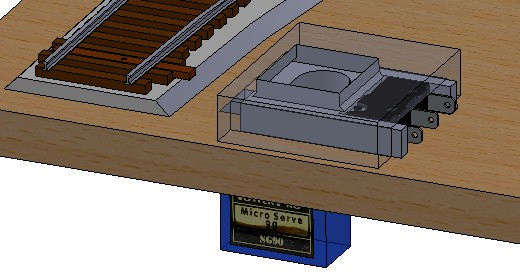
Le problème venait de la précision de positionnement. Il fallait régler
les butées (par des CV) de façon extrêmement précise. Ceci s'est avéré
assez peu pratique.
J'ai donc pris le parti de ne plus toucher aux butées du servomoteur et de laisser le débattement à 180°.
Le servomoteur se contente donc d'actionner un excentrique à l'intérieur d'un trou oblong.
Dans une position extrême, le trou oblong est poussé d'un coté:

Dans l'autre position extrême (à 180°), le coulisseau est poussé de 4mm environ.

En position reculée, il est possible d'appuyer sur le microswitch
Ce système est constitué d'un coulisseau mobile possédant un trou
oblong, et d'un guide ouvert sur le dessus pour faciliter l'accès à
l'axe du servomoteur.
Voici les pièces prototypées (procédé par laminage de feuilles PVC) :

Voici une première photo du système en place. Sur cette photo,
j'ai choisi de laisser l'interrupteur à l'extérieur du coulisseau de
commande.

Notez que la tige est pliée d'un coté pour l'effet "ressort".
Le bouton rouge est un bouton poussoir relié au décodeur pour basculer l'aiguille manuellement (en plus de la commande digitale)
Concernant les fils électriques : le blanc est relié au coeur
d'aiguillage, le rouge est relié au rail "+" et le bleu est relié au
rail "masse".
Sur cet assemblage, en revanche, j'ai été contraint de placer
l'interrupteur à l'endroit prévu dans le coulisseau en raison de
l'exiguïté du lieu (4cm entre 2 voies)

L'interrupteur est tout simplement cloué sur place ! Mouaip bon... y'a
plus propre ! Notez la fixation de la tige de fil de fer...sur le coté
du coulisseau.
Et pour terminer avec cette version, voici une vue générale de quelques moteurs posés sur la coulisse du réseau de l'ACMF.

7/ Encore un autre modèle.... SOUS la table !
Le dernier modèle présenté ci-dessus était VRAIMENT pratique !
L'accès à l'axe du servo et le réglage sont élémentaires.
MAIS....
c'était au-dessus de la table !
J'ai donc cherché à cacher le servomoteur, tout en conservant le même principe de commande (trou oblong)
Ca donne ça :


Le principe reste le même mais cette fois, la tige traverse la planche pour bouger la traverse mobile.
Si la course est un peu trop grande, c'est pas grave puisque la tige
métallique verticale va légèrement se déformer. Et cela va maintenir
l'effort de plaquage contre le rail. Evidemment, le talonnement n'est
absolument plus possible.
Voici une autre vue avec la tige de commande en place.
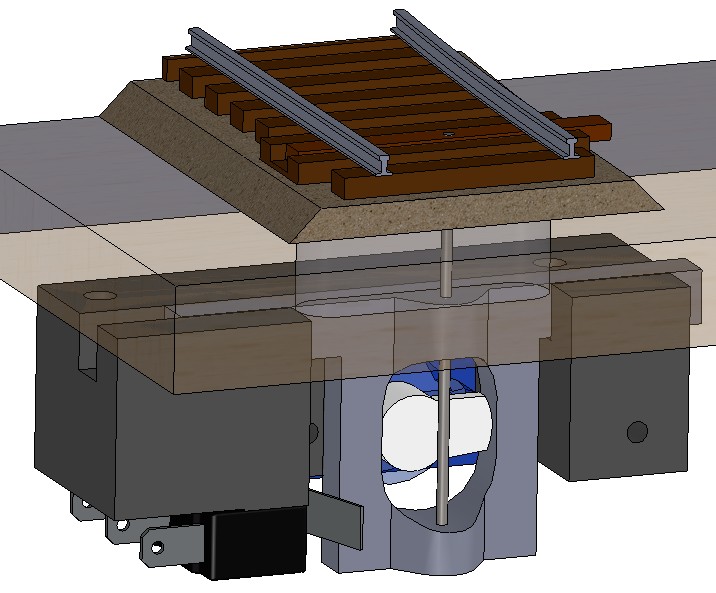
L'interrupteur
est positionné contre le plan du guide. Il permet d'inverser la
polarité du coeur d'aiguillage en fonction de la position des aiguilles.
Voici une vue depuis le dessous, qui montre les deux positions de l'interrupteur :

Reste encore à fixer cet interrupteur convenablement...
J'ai utilisé la solution rapide (mais pas très propre) de la colle
thermofusible. Je concède que cette solution n'est pas super propre...
Pire encore, le temps de la mise en place et du refroidissement de la colle, j'ai maintenu en place avec 2 clous (la honte ! 


)...
J'aurais peut-être dû utiliser 2 petites vis M3 qui auraient été bien
plus propres et suffisantes, mais je n'en avais pas sous la main à ce
moment là.
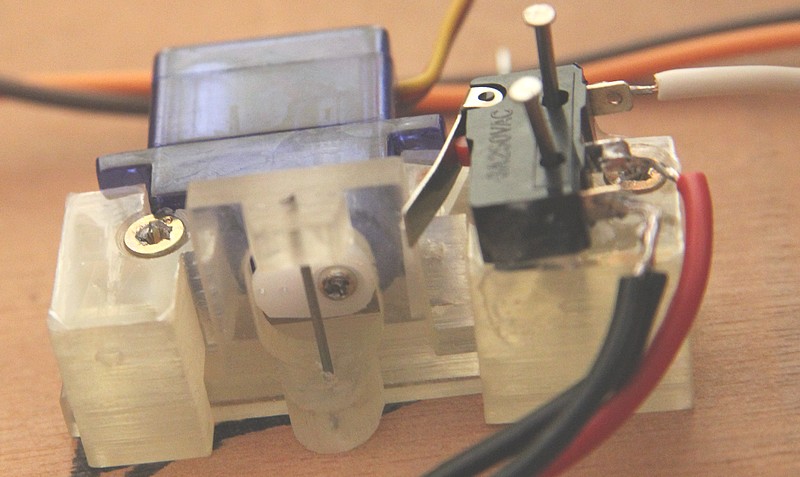

En attendant, ça fonctionne ! On verra à l'usage.
Voilou !
Comme d'hab, n'hésitez pas à me laisser un message (voir en
paged'accueil) si vous souhaitez en savoir un peu plus.