Décodeur pour
plaque tournante Fleischmann
Page créée le 05/08/2015
Mise à jour le 17/04/2017. Voir la mise à jour en bas de page
Je possède un pont tournant Fleischmann et mon club (l'AGAT à Montargis)
en possède un aussi.
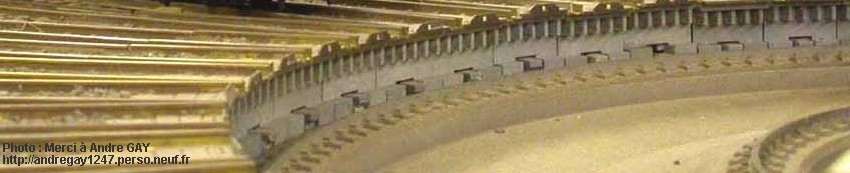
Nous souhaitions pouvoir commander ces plaques à l'aide de la centrale
digitale. L'objectif est simple :
- On appuie sur un bouton de la
centrale DCC et la plaque va toute
seule, en gérant les vitesses,
jusqu'à
la position souhaitée.
- Certains membres du club, analogiques jusqu'au
bout des doigts, souhaitent conserver une commande manuelle. Pas de
problème, on va étudier ça.
- La digitalisation permet même de faire des chose en plus, alors pourquoi se
priver ? Une lumière dans la cabine et des feux de manœuvre sur le pont
ça serait top, non?
A propos de la commande à l'aide
d'une centrale....
Il existe des centrales qui
peuvent gérer des plaques tournantes. Mon ECOS en fait partie. MAIS....
Parmi les trois plaques tournantes proposées, deux utilisent
exclusivement le protocole motorola (PAS GLOP), et la troisième est une
espèce d'accessoire hybride géré comme une loco, mais d'adresse nulle
(?!?!!?), qui n'apparait ni dans la liste des accessoires, ni dans la
liste des locos.... bref,...pas clair! et donc...PAS GLOP!.
J'ai donc choisi de faire un décodeur utilisable par TOUTES les
centrales DCC. Les différentes actions seront gérées comme des
accessoires (voir plus bas).
Sommaire de cette page :
1/ Analyse du fonctionnement :
Pour ce décodeur, il va y avoir une partie d'électro-mécanique.
L'électronique doit s'adapter à la mécanique !
Ne sachant pas comment elles fonctionnaient, j'ai entrepris un petit
démontage de la manette de commande et de la motorisation.
Coté manette :
C'est simplissime ! il y a un pont redresseur et deux interrupteurs qui
frottent contre un circuit imprimé:

- Celui du haut est un
interrupteur inverseur à 2 positions stables,
pour inverser la polarité envoyée au pont (fils Jaune+Rouge).
- L'autre est un interrupteur à 3 positions : une position
centrale par défaut et 2 positions momentanées, pour le maintien de la
bobine du pont (fil Gris)
Coté motorisation :
C'est déjà plus..."sympa" :
Le démontage du pont est
assez facile : Au centre du pont, il faut soulever une plaque centrale,
il y a un circlip à enlever, et le pont vient sans résistance
.
Les 5 palpeurs frottent sur 5 pistes circulaires. Ainsi, la plaque peut
faire autant de tours que voulu sans emmêler les fils.
Les 2 palpeurs de gauche sont directement soudés sous les rails. Les 3
autres contrôlent la motorisation.

Comment ça marche???? SIMPLE !!!! :
- Le fil gris n'alimente
directement QUE la bobine qui
déverrouille l'index gris clair(horizontal).
- Ce déverrouillage ferme le contact de l'interrupteur
- La tension venant des fils Jaune+Rouge peut ainsi alimenter le
moteur (avec la bonne polarité, donc dans le sens voulu)
- La roue motrice peut donc
tourner. Les 4 creux tournent avec elle ==> il n'est plus nécessaire
de maintenir la bobine.
- Tant qu'aucun creux n'est en face de l'index, celui-ci ne peut
revenir en position initiale, il maintient donc le moteur en marche.
- Dès qu'un creux se présente, l'index plonge dedans. Il ouvre ainsi le
contact, ce qui arrête le moteur...au bon endroit !
Les 4 creux sont judicieusement placés : 1/4 de tour de la roue motrice
correspond exactement à un écart de voie. Ainsi, lorsque l'index est
enfoncé dans un creux de la roue, il maintient le pont en face de la
voie voulue.
C'est à cause de cet index et de la bobine qu'on entend le fameux
"CLAC" CLAC" si caractéristique de cette plaque.
Le levier de débrayage a 2 fonctions :
- poussé vers la droite (voir
photo ci-dessus) il déverrouille l'index et provoque la rotation du
moteur. Le pont peut avancer. le sens de rotation dépend du dernier
sens utilisé avec la manette.
-
tiré vers la gauche, il recule l'ensemble de la motorisation et débraye
l'engrenage, permettant ainsi de régler la position exacte du pont en
face des voies. Dans cete position, le moteur ne tourne pas.
Coté schéma électrique, voici ce que ça donne :
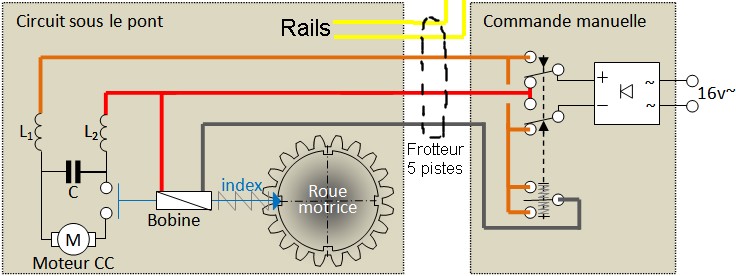
Au niveau du frotteur central voici les connections (vues depuis le
dessous du pont) :

Maintenant que le fonctionnement est clair, je peux me pencher sur les
moyens de commander tout ça...
2/ Digitalisation :
Comment digitaliser tout ça ??
?? Zatizeukouétcheune !
2
solutions sont possibles :
Soit je place un décodeur en
dehors de la plaque tournante, soit je
l'intègre dans le
pont tournant. Chaque solution a ses avantages et
inconvénients :
La première solution (décodeur
en dehors) paraît séduisante par sa simplicité mais elle ne me
plait pas trop :
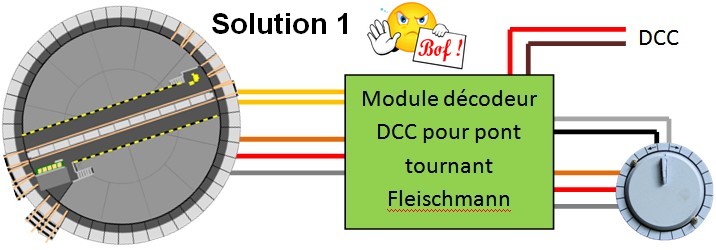
Certes, elle est simple à
mettre en place puisqu'il n'y a que les 5
fils de la plaque à brancher. Mais c'est là tout le problème ! il n'y a
QUE
5 fils ! La commande de fonctions annexes et la vérification de la
position réelle est impossible. Le positionnement n'est basé que sur le
décompte du temps
entre deux
positions. PAS GLOP ! Il est vrai que le système d'indexage décrit plus
haut peut
permettre une bonne flexibilité mais il faut avoir une confiance
absolue dans la vitesse du moteur. Et ce n'est absolument pas le cas
pour ma plaque : ça ne tourne PAS DU TOUT à vitesse constante malgré la
révision générale. L'inversion de polarité du pont fait toujours appel
à un module de détection de court-circuit. J'aime pas ! Et j'en ai pas.
La seconde solution (décodeur
DANS le pont) est bien plus compliquée à réaliser mais me paraît plus
intéressante :
En théorie, seuls les fils DCC (jaunes) sont strictement nécessaires.
Les trois
autres sont superflus, on peut les utiliser pour conserver une commande
manuelle...(Good!!)
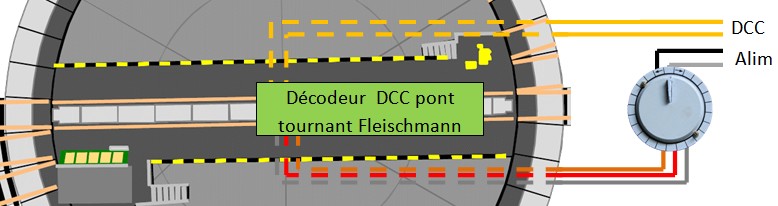
Cette solution permet d'ajouter quantité de petites choses :
- Positionnement basé sur le comptage des voies, aucun risque
d'erreur. 
- Vitesse variable à volonté
(accélération progressive, freinage anticipé, valeurs maxi-mini
programmables...)
- Feux (clignotants ou pas)
aux extrémités du pont, (rouge-vert possible)
- Lumière dans le poste de
commande, pilotable par DCC ou en commande manuelle.
- Polarité des rails du pont
programmée en fonction des voies abordées (programmable)
Solution adoptée !
Schéma
électrique :
Voici donc le circuit que j'envisage : 
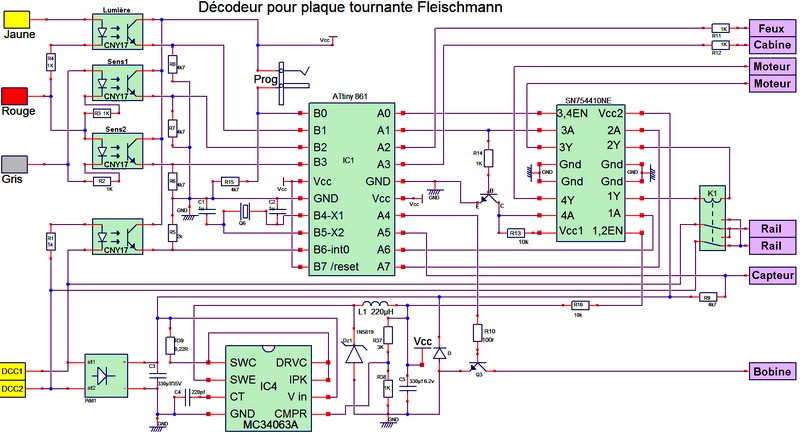
Waouh !
Ça fait beaucoup de composants !
Ce
qui me fait peur, c'est la largeur disponible sous le pont. Je n'ai que
28mm, pas un de plus. Ça va être la crise du logement...
En revanche, j'ai 130mm disponibles en longueur. Je sens qu'il va y
avoir du strap...
Ce circuit contient :
- le µC atmel ATtiny861, cadencé à 16MHz.
- Un driver de moteur SN754410NE pour
gérer le moteur en MLI (La vitesse est bien plus facile à contrôler !).
Il permet aussi de contrôler le relais bistable dans les deux sens.
- Un relais bistable avec une
seule bobine polarisée, pour changer la polarité des rails du pont.
- Une alimentation à découpage
(MC34063A)
- Trois optocoupleurs pour
recevoir les instructions de la commande manuelle, plus un pour le filtrage du signal
DCC.
Et comme on ne peut rien vous cacher, vous avez remarqué une entrée
spéciale : "Capteur". Bravo !
Ça, c'est pour la bonne synchronisation
du bébé. J'ai prévu de placer un capteur à effet hall près de la roue
pour
compter le passage des voies. (voir
plus bas)
3/ Réalisation et implantation :
Le typon :
Après 4 heu non 8... 17 jours de
maux de tête
, deux composants bien cramés
,
et de nombreuses versions successives
pour faire rentrer tout ça dans
l'espace réservé, j'obtiens l'implantation ci-dessous. Cerise sur le gâteau,
j'ai même pu diminuer la longueur de l'ensemble.
Avec l'espace pour les frotteurs, j'obtiens un circuit de 28mm*103mm.
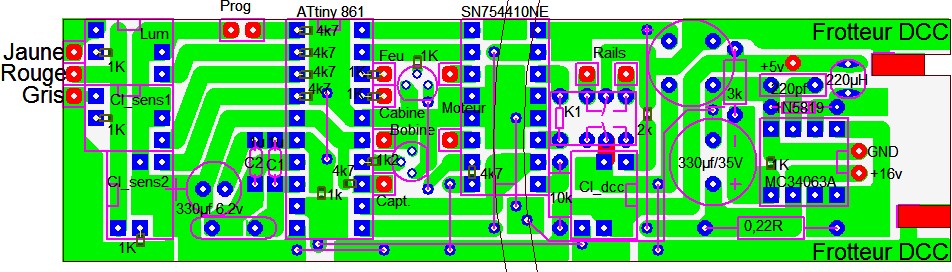
Les pastilles colorées en rouge sont les points sur lesquels je vais
faire les branchements.
J'ai fait figurer la position du rail central de la fosse car à cet
endroit, il n'y a quasi aucun dépassement possible. Le circuit doit
être extra-plat. C'est pour cela que je n'ai pas utilisé de support
pour le SN754410.
Notez la forme particulière des deux pastilles "Frotteur" (rectangle de
2.5mm*6mm). Elles vont
recevoir les frotteurs du pont tournant. Je vais donc devoir démonter
les frotteurs soudés sous les rails, pour les souder contre mon circuit
imprimé (voir plus bas).
Pour pouvoir tout rentrer, j'ai eu recours aux résistances CMS et à de
nombreux straps.
Le typon officiel est disponible ici en pdf:
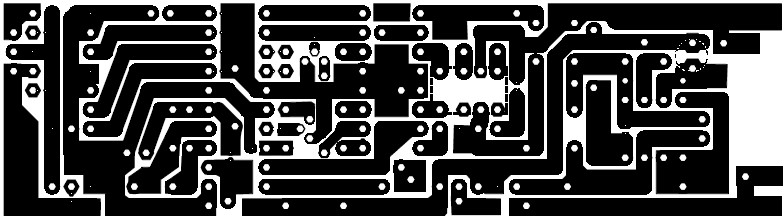
La méthode est classique : Insolation, révélation, gravure au
perchlorure de fer.
Dans cette plaque, je réalise 2 gros trous pour le relais CMS (disponible ici) et la
bobine CMS (disponible ici), pour éviter qu'elles ne dépassent trop. Il
était impossible de les souder sur la face "cuivre" en raison de leur
épaisseur. j'aurais été perdant.

La photo ci-dessous montre la version "0" avec les composants en place.

Le soudage des palpeurs demande un peu d'attention. J'ai
préalablement repéré leur position exacte sous le pont avant de les "arracher"
(pas d'autre solution). J'ai reporté cette position sur le calque du
typon. Lors du soudage, le calque était dessous pour bien cibler la
position. Grâce à cela, je n'ai qu'un quart de millimètre d'écart par
rapport la position idéale.
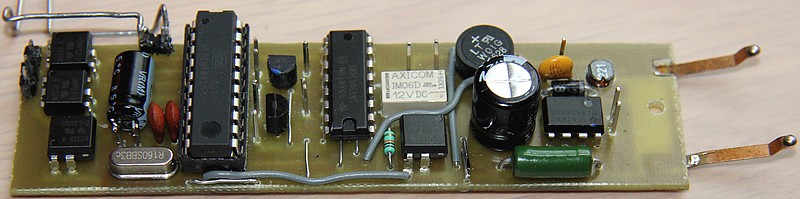
La densité de composants est relativement élevée pour des composants
standards.
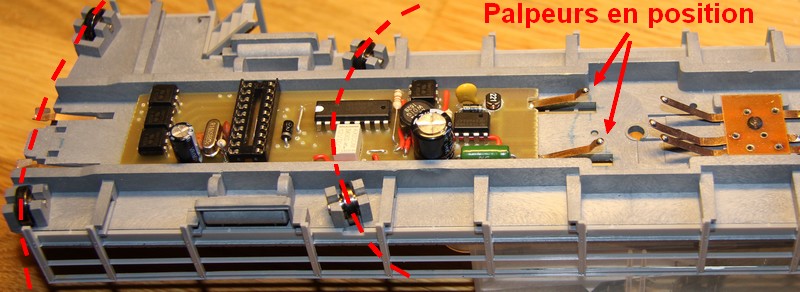
Sur la photo ci-dessus, il s'agit de la version "0". Les
deux
condensateurs dépassaient. Sur la version finale, il n'y a plus que le
gros condensateur de droite qui dépasse. Mais là, je n'ai pas
trop le choix.
Remarquez sur cette photo que j'ai dû prendre garde à la hauteur des
composants situés au niveau du rail central (figuré en pointillés).
Vous comprenez maintenant pourquoi j'ai utilisé un relais CMS. Dans la
première version, j'avais utilisé un relais bistable standard.....mais
ça coinçait carrément.
4/ Mise en place des divers éléments :
La lumière
de cabine :
Là, c'est très facile ! Surtout que la cabine possède un petit coffre
qui recouvre un passage bien utile :
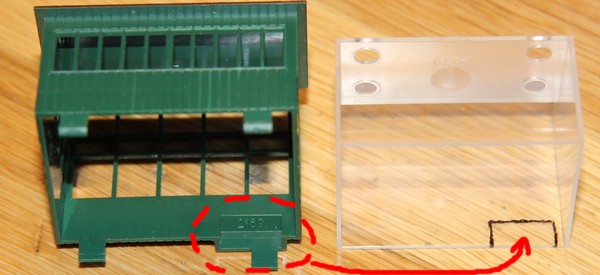
Je vais profiter de ce petit vide pour installer un connecteur
automatique.
Ni une ni deux, je soude deux fils émaillés sur une LED CMS, et je la
colle au plafond. Je fais passer les câbles dans les coins et je
rejoins les deux palpeurs.
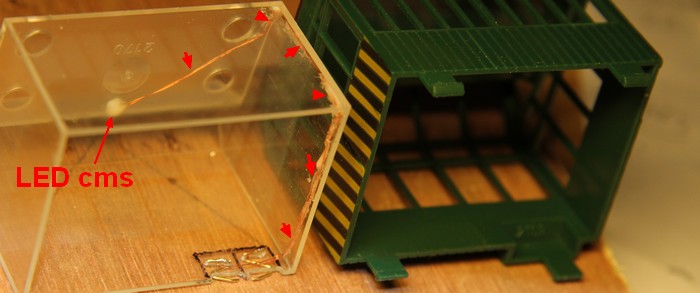
Ces palpeurs sont en fil de laiton, diamètre 0.4mm. Pour chaque
palpeur, j'ai percé 2 trous dans le plastique transparent et j'ai tordu
le fil en laiton pour faire "ressort". Au passage, j'ai gratté un peu
le plastique pour que les plaques de contact puissent passer.
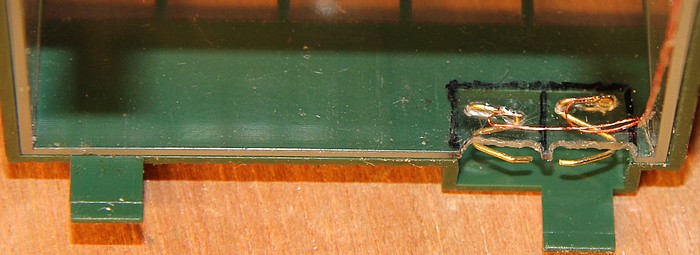
Ça tient nickel dans "le coffre" !
Sur le pont, je colle donc 2 plaques en laiton juste sous le "coffre".
Un bonne goutte de cyano' est suffisante pour les maintenir en place.
Je précise que j'ai dû agrandir la rainure déjà présente pour faire
passer la seconde plaque.(visible sur la photo).

Les 2 plaques sont issues des restes d'une grappe en laiton d'un kit.
Je les ai découpées, mises en forme et pliées.
Le petit téton doit dépasser dessous pour connecter un fil.

Ensuite, je replace la cabine dans les trous prévus à cet effet.
Le contact se fait automatiquement. Elle reste démontable à volonté.
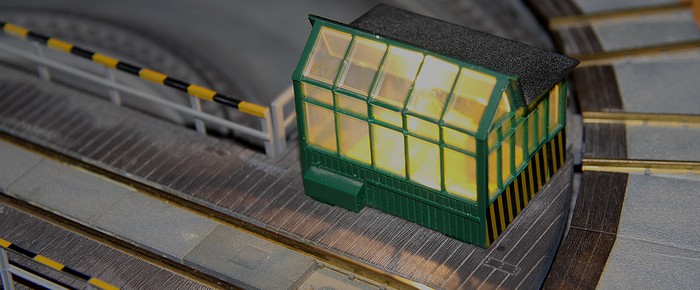
La lumière est bien suffisante. Sur cette photo, le flash n'a pas suffi
à la masquer.
En revanche, sans flash, ça fait un peu phare à iode... la photo n'est
pas super fidèle.
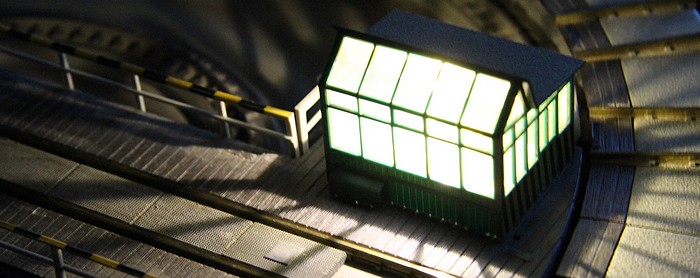
En réalité, la teinte est beaucoup plus agréable.
Le feu
d'extrémité de pont :
Là, on fait simple. De toute façon, le µC ne pourra pas gérer plus d'un
feu (ou alors deux fois le même ou deux couleurs en alternance). Le
circuit décrit plus haut est prévu pour une seule LED par
signal. Il est possible d'en installer deux en faisant une petite
variante. Dans ce cas, la résistance cms qui se trouve à la sortie du
µC sera shuntée (voir plus bas).
Je prends donc le signal vendu avec la plaque tournante et je tranche
dans le vif : craaaac !

Je perce deux trous juste sous les casquettes.
Sous le guidon d'arrêt (casquette en haut à droite) j'installe une LED
CMS violette (pour le carré violet), tandis que sous la casquette
inférieure, j'installe une miniLED
CMS blanche. Et je fais sortir les
fils émaillés derrière.
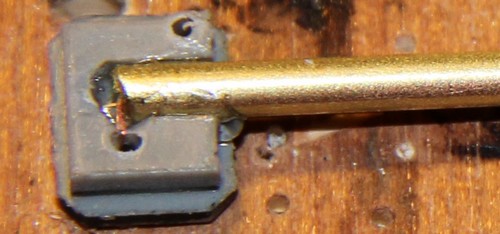
Les fils rentrent dans un tube en laiton de 2mm extérieur. Ça laisse
largement la place pour passer plein de fils à l'intérieur si
nécessaire.
Le second trou sera utilisé pour la fameuse led blanche de manœuvre.
Je découpe le panneau et je le colle sur le tube.
Je perce l'emplacement du pont au diamètre 1.9mm et j'y encastre le mât
en force sans dépasser dessous. Il ne reste qu'à raccorder les fils sur
la carte.
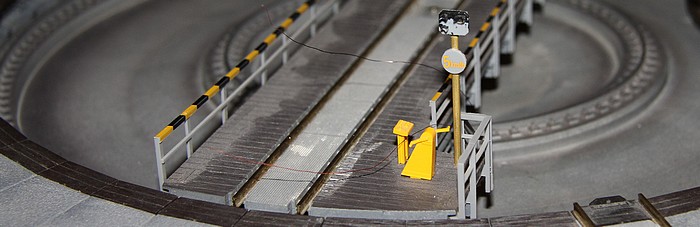
Ouai, bon ,OK, les retouches de peinture sont absolument nécessaires !
et le dépoussiérage aussi...
Si on opte pour
deux feux réversibles, la résistance de 1k2, en série avec la sortie "feu", doit
être shuntée ET reportée à l'extérieur du circuit :

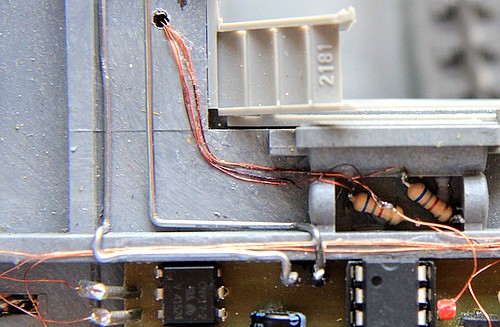
Le capteur de position :
La roue motrice se prête bien à une détection puisque c'est ELLE qui
contrôle le bon positionnement du pont face aux voies. J'y colle donc
un capteur qui va vérifier sa rotation.
Il s'agit d'un capteur à effet hall de type monostable.
C'est donc la présence d'un aimant qui va déclencher l'information de
passage entre deux voies. La précision n'est pas nécessaire, on l'a vu
plus haut. On n'a besoin que de compter les voies.
J'ai fait le choix de compter les voies au moment où on franchit la
limite entre 2 voies. C'est à dire à mi-chemin entre deux rainures
d'arrêt.
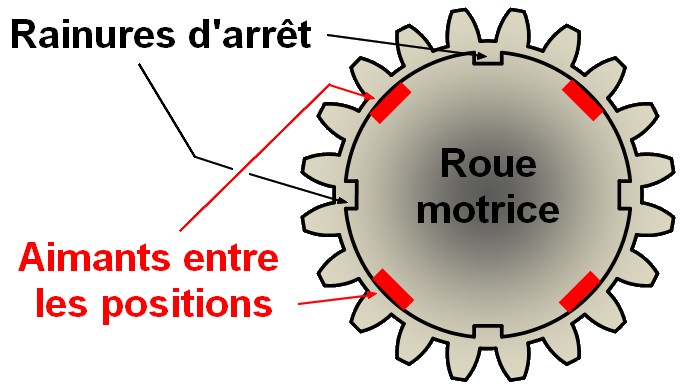
Il est donc naturel d'installer 4 aimants sur la roue motrice, à égale
distance des rainures d'arrêt.
La mise en place du capteur ne demande qu'un léger pliage et un petit
collage pour le maintenir au plus près de la roue.
- La patte du haut est reliée au
+5v
- La patte du milieu c'est la masse (GND)
- La patte du bas, c'est le signal de détection (pas d'aimant=5v,
présence d'aimant=0v)

Les quatre aimants (au néodyme, achetés sur ce site)
mesurent 1mm de diamètre par 1mm de long. Ils sont insérés en force
dans les perçages. Par sécurité, j'ajoute une goutte de cyano au verso.
Mais ça me semble symbolique voire superfétatoire...
Le
"bouton" de programmation :
Je n'avais pas la place pour un vrai bouton de programmation, et de
toute façon, il aurait été inaccessible.
J'ai donc prévu uniquement deux bornes de connexion sur la carte, et je
place ensuite deux fils dénudés l'un à coté de l'autre. Il suffit de
les mettre en contact pour lancer la procédure de programmation.
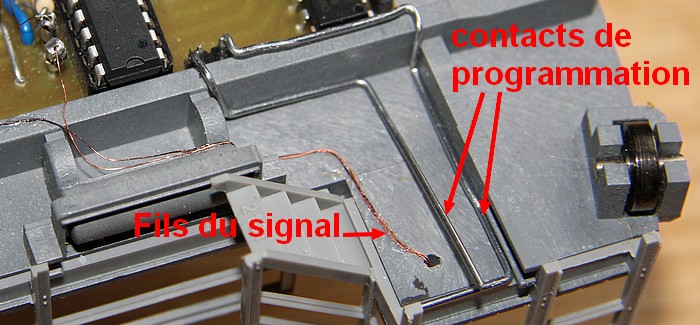
Le pliage des "fils" demande un peu de précision pour bien tenir dans
les coins. Il est solidaire de la carte. Les "fils" proviennent d'un
rouleau de fil de fer utilisé dans les gaines électriques pour tirer les fils.
(Remarque : Cette photo montre uniquement 2 fils pour le feu violet (version "0")
La version finale possède 2 résistances et 2 fils en plus pour le feu
blanc.)
Connexion des fils :
C'est une étape pas facile avec une clavicule cassée... Ça demande pas
mal de précision et la tâche est répétitive (16 fils à brancher!
).
Les deux fils gris alimentent les rails. Leur polarité est contrôlée
par le relais.
J'ai collé les fils émaillés le long de la structure du pont. J'ai
ajouté des petit connecteurs au bout de chaque fil pour permettre un
démontage de l'ensemble. Certains connecteurs ont été peints pour
mieux les identifier.

A-propos... lors du branchement du moteur, vérifiez que la plaque
tourne dans le bon sens. Sinon, inversez les fils.
De même, lors du branchement des rails, vérifiez que la polarité est
correcte pour la première voie. Sinon, inversez les fils.
5/ Programme :
Pas facile d'organiser la structure d'un programme. Surtout que la
gestion du moteur doit être EXTRÊMEMENT rigoureuse, sans quoi, on
s'expose à des expériences "fumeuses" : Un driver SN754410 ça
crame
vite !!!!...
Ce décodeur est assez différent de ceux construits précédemment,donc,
sans un minimum d'organisation, point de salut.
Je construis un algorithme qui doit m'aider à structurer le programme.
(la boule sur le fil signifie "non"). Le sous programme d'acquisition de la trame qui a été déjà détaillé ici.
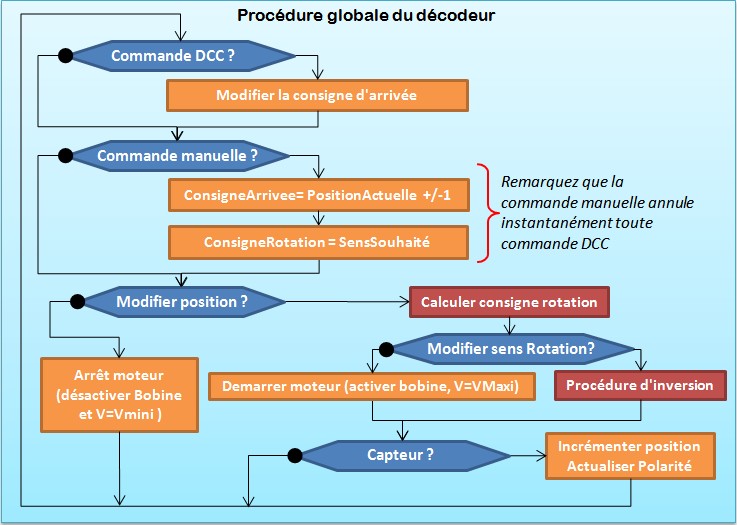
Parmi toutes ces instructions, seuls deux points sont délicats pour
l'écriture du programme :
- le calcul du sens de rotation optimal
et
- la procédure d'inversion de sens
du moteur électrique.
Voici une solution pour chacun d'eux :
1/ choix
du sens de rotation optimal
Le but de cet algorithme est de choisir le sens qui permettra
d'atteindre la voie voulue en un minimum de temps. Il faut donc tourner
dans le bon sens. On se base sur le numéro de voie de départ et
d'arrivée.
Départ = numéro de la voie de
départ
Arrivée= numéro de la voie d'arrivée.
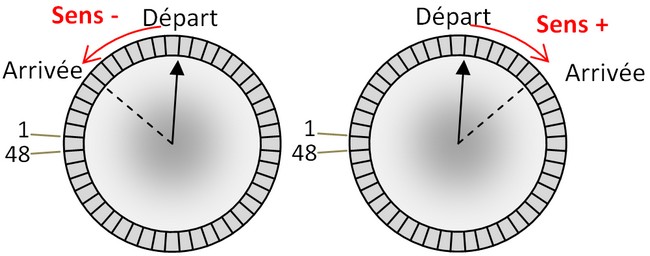
Avec 48 voies, on divise par deux...donc si l'écart est
inférieur à 24 voies c'est facile : On fait l'opération
"Ecart=Arrivée-Départ", et le sens est vite trouvé en fonction du signe
du résultat...
Oui... mais... non ! Car
1/ ça ne marche que si on ne franchit PAS les voies 1 ou 48... et
2/ le sens de l'opération n'est
pas le même si le départ est inférieur à l'arrivée (problème de signe).
3/ Il y a 2 extrémités sur un pont ! c'est donc
l'extrémité la plus proche qui doit rejoindre la voie souhaitée.
Solution ==> Le cadran doit donc être divisé en 4 secteurs et non 2 :
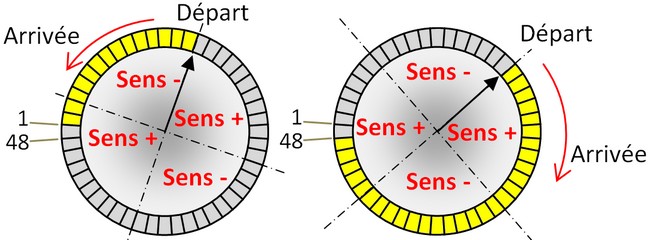
Dans le cas de gauche, si on calcule la différence "Départ-Arrivée" on
obtient les sens suivants :
Ecart = Départ-Arrivée
|
0 à 12
|
13 à 24
|
25 à 36
|
37 à 48
|
Sens
|
-
|
+
|
-
|
+
|
Dans le cas de droite, la différence "Arrivée-Départ" donne le
tableau ci-dessous :
Ecart = Départ-Arrivée |
0 à 12 |
13 à 24 |
25 à 36 |
37 à 48 |
Sens
|
+
|
-
|
+
|
-
|
Soit 8 cas en tout !
Mais en réfléchissant un peu, on se rend compte que la consigne DCC
n'envoie aucune consigne supérieure à la voie 24. L'ordre
"voie32" est identique à l'ordre "Voie8". Il faut donc ajuster la
consigne d'arrivée en même temps. J'ai mis un bout de temps à
comprendre le problème...
- Donc, dès que l'écart devient
supérieur à 11 voies, il devient intéressant de prendre la voie opposée
comme arrivée. On ajoute donc "24"
(ou retranche suivant le cas)
pour rester dans la plage [1-48].
- Si l'écart est compris entre 25 et 35 voies alors diminuer
l'écart de 24 tout de suite pour trouver la destination la plus proche.
- Pour l'écart égal à 47 voies (franchissement de la voie de
référence) on ne change rien.
Et pour terminer l'affaire, sachez que lors du retournement à
180°, tous ces calculs n'ont pas lieu d'être....le sens est indifférent.
Ainsi, pour déterminer le sens de rotation idéal et l'arrivée idéale,
on peut suivre l'algorithme suivant :

Il y a certainement plus simple, mais celui-ci fonctionne.
Ca se traduit par l'extrait de programme suivant :
2/
Inversion automatique de la rotation
En théorie, l'inversion du sens ne pose pas de problème en soi. Il
suffit
d'inverser la commande. C'est binaire. Mais ceci n'est vrai que si on
n'étudie
l'inversion de sens pendant l'arrêt du moteur.
Là où ça devient compliqué c'est quand on veut modifier le sens
de rotation du moteur PENDANT qu'il est déjà en train de tourner.
ACHTUNG ! Il faut mettre une séquence comme celle-ci si on ne veut
cramer ni le moteur ni les transistors :
1 - ralentissement jusqu'à
vitesse = 0.
2 - arrêt (désactivation bobine),
3 - une pause...même très courte (rigoureusement
OBLIGATOIRE sinon y'a un truc qui va griller quelque-part),
4 - inversion du sens,
5 - démarrage (réactivation bobine),
6 - accélération jusqu'à la vitesse maxi.
Evidemment, il n'est pas nécessaire d'effectuer cette séquence lorsque
la nouvelle consigne de sens est identique au sens actuel.
Ce qui nous amène à l'algorithme suivant :
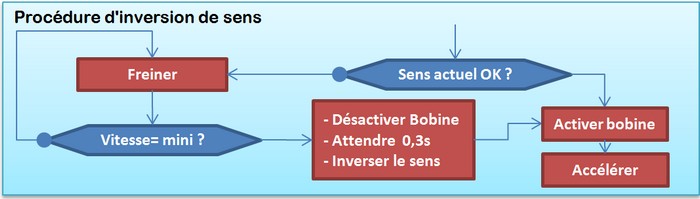
Avec ça, le programme est bien plus facile à construire.

6/ Réglage des CV
Tout décodeur DCC qui se respecte DOIT posséder des réglages. C'est
d'autant plus vrai avec une plaque tournante.
Les CV interviendront pour mémoriser :
- les voies présentes (si vous en
avez 48....mes respects...!
)
- la polarité de chaque voie (le pont doit s'adapter car chaque voie
possède sa propre alimentation)
- la vitesse maxi souhaitée (255=pleine vitesse, mais c'est franchement
rapide !)
- la vitesse minimum souhaitée (Pour la pérénité du décodeur, je
déconseille les valeurs inférieures à "36")
Remarques importantes :
- La "position 1" est la voie qui
se trouve en face du pont (coté cabine) lorsqu'on appuie sur le
levier de programmation.
- 2 voies opposées (voie 1 et 25 par ex.) doivent être câblées dans le même sens (en accord avec le pont des 2 cotés).
-
La validation d'une voie valide automatiquement la voie opposée, même
s'il n'y en a pas... (le premier qui amène sa loco vers une voie
absente, il passe par mon bureau....
)
Les numéros de CV sont répartis comme indiqué dans le tableau
ci-dessous : (ATTENTION, voir la mise à jour du 17/04/2017)
CV
|
Élément
contrôlé
|
Valeur
par défaut
|
Valeurs
possibles
|
cv513
|
Vitesse mini
|
36
|
0 à
Vmaxi
|
cv514
|
Vitesse maxi
|
255
|
Vmini à
255
|
cv515
|
Taux d'accélération
|
4
|
1 à 10
|
cv516
|
Taux de freinage
|
4
|
1 à 10
|
cv517
à cv540
|
validation des voies 1 à 24
|
1
|
0 ou 1
|
cv541
à cv552
|
polarité des voie 1 à 12
|
0
|
0 ou 1
|
cv553
à cv564
|
polarité des voies 13 à 24
|
1
|
Pour la polarité, il faut observer lorsque la cabine est en face de la
voie : si les polarités du pont et de la voie sont identiques, alors la
CV vaut 0. Dans le cas contraire, c'est 1. Il n'est pas nécessaire de
configurer la polarité des voies non validées.
Par exemple, avec les voies ci dessous, les CV sont configurées ainsi
(en rouge et en bleu):
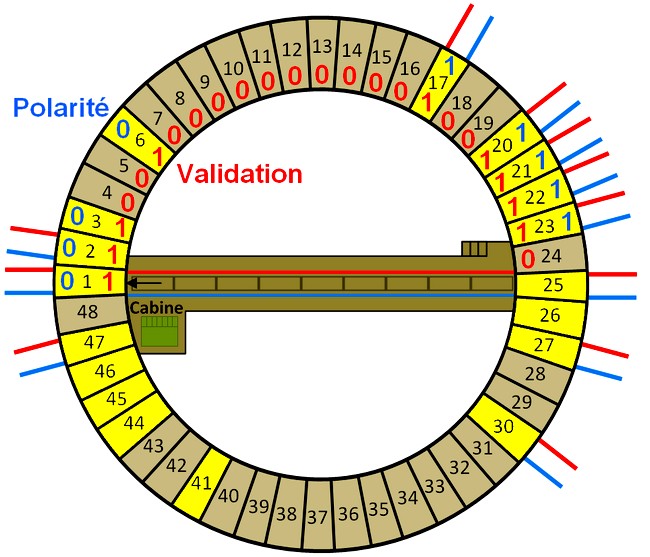
Dans cet exemple, on valide la voie 6 car on en a besoin pour la voie
30.
7/ Utilisation :
Pour contrôler la plaque tournante, 2 possibilités : La commande
manuelle... et la commande DCC.
=> Coté commande manuelle, rien ne change à part le petit
interrupteur qui commande l'allumage de la cabine.
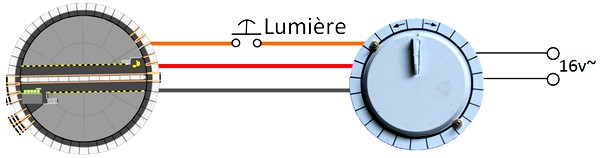
L'alimentation peut aussi être du 12v continu ou même du 5v continu. Le
sens de branchement importe peu.
=> Coté commande DCC, voici comment organiser vos accessoires sur la
centrale :
- Le premier accessoire, c'est
l'allumage (ou l'extinction) de la cabine.
- Le second
accessoire, c'est la commande du feu (forçage "Manoeuvre" ou "Carré
Violet")
- Le troisième
accessoire permet le retournement à 180°, quelle que soit la voie.
- Les accessoires suivants indiquent la voie souhaitée.
Par exemple, pour la configuration ci-dessus, voici ce que ça donne sur
l'écran de l'ECOS :
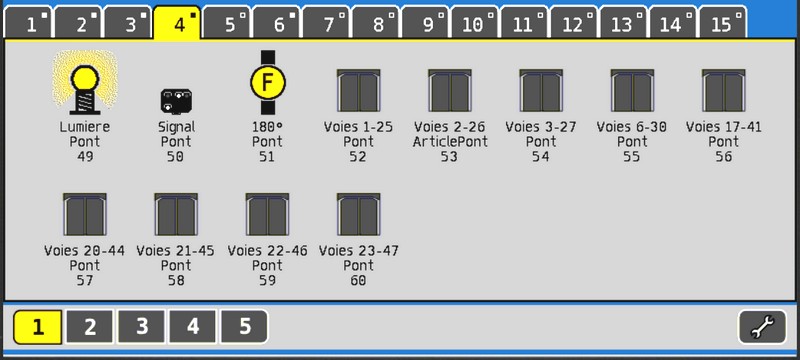
Il est crucial que les adresses d'accessoires se suivent (49, 50,51,52,etc...) dans
l'ordre.
- Un appui sur une voie démarrera
la plaque pour s'aligner dessus. Un nouvel appui sur cette voie ne
provoquera aucun mouvement.
- Chaque appui sur la lumière (de cabine) inversera son état.
- Chaque appui sur le signal inverse son état (uniquement si le pont est immobile dans le cas contraire, c'est violet.)
- Un appui sur le "retrournement à 180°" provoquera le demi-tour du
pont.
La programmation est vraiment simple :
Un seul appui sur le levier de programmation permet de régler
l'adresse de base du décodeur.
- Le feu du pont tournant se met
alors à clignotter.
- Il suffit de commander le premier accessoire (la lumière) depuis
la centrale pour que le décodeur mémorise l'adresse. C'est
fini !
- Si
vous ne souhaitez pas modifier l'adresse, vous pouvez appuyer de
nouveau sur le levier de programmation. Cela provoque le
changement de
référence de voie. C'est la voie qui se trouve, à ce moment-là, en face
du
pont (coté cabine) qui servira de voie numéro 1.
La
vidéo :
8/ Mise à jour du 17/07/2017:
Suite à une sollicitation d'un internaute, et aussi
parce-que je rencontrais un petit souci technique, j'ai revu
entièrement le programme de la plaque tournante.
La partie physique n'a pas évolué. Elle marche très bien, il n'y a pas de raison majeure d'y toucher.
En revanche, le programme méritait d'être optimisé car j'étais très
proche ds limites du µC. Celui-ci ne recevait pas correctement le
signal DCC. C'est d'ailleirs visible sur la vidéo ci-dessus...je suis
obligé d'appuyer plusieurs fois sur le bouton pour la plaque réagisse.
Problème résolu !!!
J'ai passé quelques nuits à me casser la tête sur le programme et j'ai
réussi à optimiser le fonctionnement. Voici la liste des améliorations
:
- Temps de réaction immédiat
- Diminution du nombre de variables.
- Diminution de la fréquence d'alimentation du moteur
- Saisie de la trame DCC uniquement sur fonts montants
- Calcul de la position d'arrivée uniquement lors de la réception d'un ordre de mouvement.
- Calcul du sens optimal lors de la réception de l'ordre de mouvement.
- Taille du programme réduite.
Cerise sur le gâteau, j'ai aussi ajouté une CV pour différencier la
vitesse minimum en fonction du sens de rotation. Je me suis rendu
compte que ma plaque n'avançait pas du tout à la même vitesse suivant
qu'elle tourne "vers la droite" ou "vers la gauche". A haute vitesse le
problème n'apparaît pas, mais à faible vitesse, la différence est
notable. Ainsi, il est possible de régler au plus juste, et de façon
indépendante, la tension de "vitesse lente".
Les nouvelles CV répondent donc à ce nouveau tableau :
CV
|
Élément
contrôlé
|
Valeur
par défaut
|
Valeurs
possibles
| clignottement signal
|
cv513
|
Vitesse mini sens 1
|
63
|
0 à
Vmaxi
| 1 fois
|
cv514
|
Vitesse mini sens 2
|
63
|
0 à Vmini
|
cv515
|
Vitesse maxi
|
255
|
Vmini à
255
| 2 fois
|
cv516
|
Taux d'accélération
|
4
|
1 à 10
| 3 fois
|
cv517
|
Taux de freinage
|
4
|
1 à 10
| 4 fois
|
cv518
à cv541
|
validation des voies 1 à 24
|
1
|
0 ou 1
| 5 fois
|
cv542
à cv553
|
polarité des voie 1 à 12
|
0
|
0 ou 1
| 6 fois
|
cv554
à cv565
|
polarité des voies 13 à 24
|
1
|
Notez que j'ai aussi ajouté le clignotement du signal lors d'une programmation de CV. Ca permet d'être sûr...
Enfin, je remercie José pour le schéma ci-dessous. C'est le schéma de câblage entre la platine électronique et les différents composants :
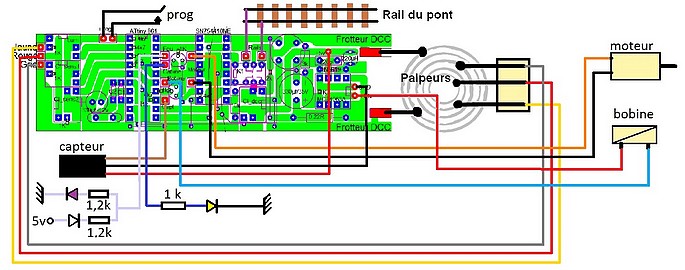
C'est une excellente idée ! Je n'avais pas pensé à le dessiner tellement j'étais pris par le reste de la mise au point.
En résumé :
- La bobine est branchée entre le +16V et le plot "bobine". La polarité n'a pas d'importance.
- La cabine est branchée entre le plot "cabine" et la masse (fil noir). Ne pas oublier la résistance et attention au sens.
- Le signal à 2 feux est branché entre 5V et masse. Le plot "Feu"
est branché entre les 2 résistances. Attention au sens de montage.
- Le capteur reçoit le 5V, la masse, et le fil signal est connecté au plot "capteur". Voir le datasheet du composant pour la polarité sinon CRZRZOUIC !
- Les 3 palpeurs de commande manuelle sont connectés à l'opposé de la plaque. Ouai, je sais, c'est pas pratique.
- Le moteur est connecté sur les deux plots "moteur" situés à coté du SN754410NE.
- Les deux rails du pont sont reliés aux sorties du relais sur les plots "rails".
C'est tout pour aujourd'hui. Evidemment, je me ferai un plaisir de
répondre à vos questions.
laissez vos
impressions par mail (après avoir enlevé les 3 "z" de l'adresse)
A vous de jouer !