Grue 50T CAILLARD - SMD
motorisation et digitalisation

Et oui ! C'était ça la surprise ! Mais vous vous en doutiez
certainement...Comme d'hab', je n'ai pas résisté à l'envie d'ajouter
des choses !
Cette page décrit comment je m'y suis pris pour motoriser l'ensemble et
comment j'ai résolu les différents problèmes rencontrés,
afin que vous puissiez vous lancer dans cette digitalisation en sachant
ce qui vous attend.
Sommaire de cette page :
1/ Matériel nécessaire :
Vu le temps que j'ai mis pour réunir tous les composants, je vous
simplifie la tâche en faisant une liste à-peu-près exhaustive :
- Couple conique 10/25 (lien ici) 9,43€
- Engrenage parallèle 10/75 (lien ici et ici) 3,31€ + 7,40€
- 1 motoréducteur 12v - 30tr/min (lien ici) 2,40€
- 3 motoréducteurs 12v - 180tr/min (lien ici) 7,20€
- Pièce prototypée (fichier stl téléchargeable)
- 1 vis M2*16 + écrou autofreiné (lien ici) 0,02 €
- 6 vis M2*12 + 2 écrous M2 0,10€
- Tube en laiton D=4mm d=2mm, L=4cm 0,11€
| - Tube ou tige en laiton D=2mm L=10cm 0,09€
- Circuit imprimé épaisseur 0.5mm (lien ici) 0,4€
- Décodeur de locomotive 21 broches ==>21€
- Support 20 broches (lien ici) 0,89€
- Fil de pêche tressé 0.16mm (rayon pèche Décathlon) 2€
- 2 relais 2RT monostables miniatures (lien ici) 8€30
- Plombs de pêche de 6g et 10g (rayon pèche...). 2€
- 3 poulies de 4mm, largeur1.6mm (lien ici) 4€80
|
Difficulté : moyenne
Outillage : Rien de spécial en dehors de l'outillage classique du modéliste. Prévoir 2 perceuses (ou un tour)
Budget : 70 euros, y compris le décodeur 21 broches
2/ Recherche de solutions :
D'abord, déterminer quels mouvement je vais pouvoir effectuer
- La rotation de la tourelle par rapport au châssis,
- La montée-descente de la flèche.
- la montée-descente du crochet principal
- La montée-descente du crochet secondaire.
Puis trouver les moteurs qui ont une chance de rentrer dans la cabine
en offrant des vitesses et des couples acceptables. Mon choix s'est
porté sur ces moteurs là, qui sont petits, costauds, pas chers et
existent avec plusieurs rapports de réduction. La présence d'un arbre "long" est aussi un avantage pour faire les treuils.

J'utilise
des moteurs "rapides" (180 tours par minute) pour les treuils et un
moteur "lent" (30 tours par minute) pour la rotation de l'ensemble.
Plusieurs dispositions possibles :
J'ai commencé par étudier la disposition des éléments en modélisant la
cabine et les moteurs. J'avais plusieurs solutions :
Solution 1 :
- 3 moteurs pour 4 mouvements... ça va pas le faire.
- Et c'est pas super compact, il y a beaucoup de place perdue.
-
Le moteur est très avancé pour placer un couple conique
directement sur l'axe de rotation de la cabine. Mais la place
manque entre les flancs des treuils.
PAS GLOP
|  |
Solution 2 :
Là, c'est plutôt pas mal mais les deux poulies situées à coté du pignon
cônique sont un peu basses. J'aimerais pouvoir enrouler une grande
quantité de fils mais là les enroulements vont être gênés. Et je n'ai pas de place pour fixer l'ensemble sur la plaque.
PAS GLOP
|  |
Solution 3 :
- Les trois poulies sont situées en haut, et suffisamment dégagées du
pignon conique et j'ai largement de quoi placer des vis par
dessous. c'est plutôt bien.
- Mais les deux moteurs latéraux débordent du gabarit au niveau du toit.
PAS GLOP !
|  |
Solution 4 :
- Là, les 4 moteurs tiennent bien à l'intérieur de la cabine.
- Le décodeur rentre tout juste au-dessus.
- Mais les éléments de transmission du mouvement de rotation de la
cabine ne vont pas être simples à placer. Il faut que le moteur qui
assure la rotation de la cabine se situe dans le plan de symétrie de la
cabine.
PAS GLOP
|  |
Solution 5 :
C'est un compromis par rapport à la solution 3.
- Les 3 poulies sont suffisamment dégagées du pignon conique,
- L'ensemble est assez compact avec beaucoup de place au plafond.
- le gabarit n'est pas engagé
- Il reste plein de place pour le décodeur au-dessus et à l'arrière.
adoptée !
| 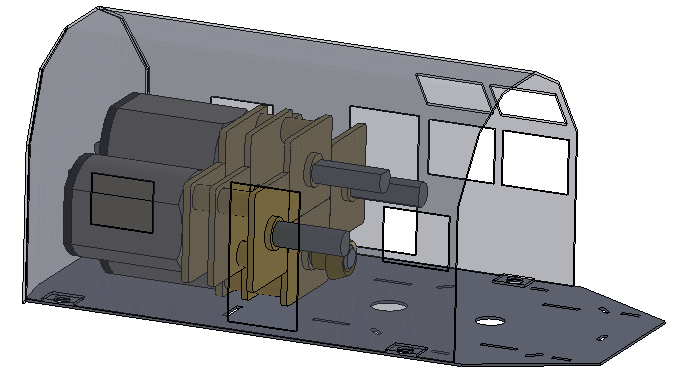 |
3/ La rotation de la cabine :
J'ai commencé par mettre en place le mouvement de rotation de l'ensemble autour de l'axe vertical :
La vitesse de rotation a été l'élément prépondérant. Le plus lent des
moteurs donnait 30 tours par minute. Il était impensable de tourner à
cette vitesse là !
J'ai donc inséré un réducteur complémentaire. L'axe du
moteur étant horizontal, j'avais besoin d'un couple conique. Mais le
rapport de réduction n'était encore pas suffisant et la place
disponible entre les deux supports de treuils était insuffisante. J'ai
donc dû ajouter un engrenage intermédiaire pour éloigner le couple
conique vers l'arrière.

Evidemment, si vous avez déjà monté les détails du kit situés à l'arrière de la cabine, il est absolument nécessaire de les démonter !
Les
deux écrous maintiennent le pivot central SANS SERRER, sinon ça coince
! Il faut juste se débrouiller pour minimiser le jeu. La version définitive
utilise un seul écrou frein M2.
Au final, j'ai un couple conique 10/25, acheté ici pour 9€43 et un engrenage10/75 module 0.3, achetés ici pour 3€31 et 7€40. Ce qui donne le rapport de
réduction suivant :
Ratio = 10/25 * 10/75 = 1/18.75.
La vitesse de rotation sous 6 volt va donc donner NCabine = 30 / 18.75 = 1,6 tours par minute

Ca me plait ! On y va !
Je commence par l'axe moteur :
Le pignon conique est réduit
en longueur, puis inséré/collé sur l'axe moteur, lui-même réduit à 2mm
de diamètre. J'ai réduit le diamètre à l'aide d'une meule de Dremel,
tout en faisant tourner le moteur sous 12v. Le résultat est
satisfaisant mais l'utilisation d'un tour est plus propre.

Attention à ne pas coller le pignon avec le bâti. Attention aussi à ce
que la colle ne pénètre pas dans l'articulation de l'axe moteur.
Globalement, soyez TRES minutieux et parcimonieux sur la quantité de
colle. L'utilisation de la cyano permet de gommer les imperfections de l'usinage "maison".
Ensuite, la grande roue conique doit pouvoir être insérée entre la plaque de base et le pignon du moteur. Il faut donc
diminuer son épaisseur pour qu'elle engrène "à la bonne hauteur". Elle
est donc raccourcie par essais successifs pour trouver la bonne
dimension. Attention, le plan ainsi réalisé doit être parfaitement
perpendiculaire à l'axe du trou.

ASTUCE : L'usinage des pièces nécessiterait un tour mais je n'en ai pas ! J'ai
fait avec les moyens du bord : Une perçeuse, un disque à tronçonner et
éventuellement quelques limes fines.
Le pignon de 10 dents est enfilé sur un bout de fil en laiton de 2mm de diamètre préalablement réduit à 1,5mm de diamètre.

Puis on enfile le tout et on soude...en évitant toute coulure de soudure dans les dentures !!!! dur dur !

Le tube de 4mm doit impérativement dépasser sous la roue conique
(épaulement de 0.3mm) afin d'assurer le centrage avec le châssis. Le
petit pignon est ensuite raccourci à 1mm de long (même technique que
précédemment).

J'utilise le ressort pour exercer un effort de maintient
sur la roue conique (4,5N maxi). Je l'ai récupéré dans les restes
d'une vieille imprimante démontée il y a bien longtemps. Il mesure
4.1mm de diamètre intérieur, 5.1mm de diamètre extérieur avec un fil de
0.5mm. La longueur n'est pas cruciale. Il faut seulement pouvoir le
comprimer à 5mm de long au minimum avec un effort modéré.
J'aurais pu me passer du ressort en réalisant une pièce prototypée qui
assure le positionnement axial précis.... mais les tolérances sur le
prototypage ne me permettaient pas de garantir le bon contact de
l'épaulement ci-dessus. J'ai préféré garder le ressort, quitte à le recouper légèrement si nécessaire.
A son tour, le pignon de 10 dents engrène avec la roue dentée de 75
dents située sous la cabine et fixée au châssis. J'ai creusé un
chanfrein à 45° du coté du bossage pour y insérer une vis M2 de 16mm de
long à tête fraisée. Cette vis sert à la fois de pivot (oui je
sais c'est pas génial) et de maintien en position pour les deux écrous
supérieurs.

Pour qu'elle soit à la bonne hauteur, j'ai soudé trois cales de 0.3mm dessous (issues des restes des grappes en laiton du kit).
En place sous la cabine, il ne reste plus qu'à tracer
PRE-CI-SE-MENT (!!!!!!!!) l'emplacement du perçage pour le pignon
de 10 dents :

Notez que je n'ai pas placé la huitième fausse-roue pour laisser le passage du pignon de 10 dents.
4/ L'alimentation en courant :
Cette roue de 75 dents possède une seconde fonction importante : l'alimentation en courant .
Pour réaliser cela, je l'ai usinée pour réaliser 2 rainures de 0.7mm de
profondeur, par 3mm de large. La roue dentée faisant 1.4mm d'épaisseur,
il ne reste que 0.7mm, mais la rigidité de l'ensemble est largement
suffisante.

N'ayant toujours pas de tour, j'ai utilisé ma bonne vieille perceuse et
une lime fine. Ca marche plutôt bien ! C'est donc à la portée de tout
bricoleur. Il n'y a pas besoin de matériel compliqué. L'utilisation
d'un tour donnera juste un résultat plus propre.
Dans ces rainures, j'insère deux bouts de circuits imprimés
découpés sur-mesure. Ce sont des circuits simple-face avec un support
en époxy de 0.5mm d'épaisseur. Ils sont collés au fond à la colle à bois.

J'ai donc 2 pistes sur lesquelles je peux faire frotter 2 palpeurs.
Les deux trous de 1.5mm sont réalisés dans les 2 pièces à la fois, en place sur le châssis :

J'ai réalisé deux palpeurs à partir d'un tube de laiton de diamètre 2mm
(ça marche aussi avec une barre pleine ). Ils sont guidés verticalement dans la pièce prototypée, juste en face de
leur piste respective. Ils reçoivent une petite rainure
à leur sommet pour y glisser une tige de fil en laiton (une corde à piano est préférable) qui servira de ressort pour bien
appuyer les palpeurs contre les pistes. Les 2 fils de laiton (ou corde à piano) seront "plantés" dans l'épaisseur de la pièce et sollicités en flexion.

L'ensemble ci-dessus est en place pour les essais avec une première version de la pièce prototypée.
Dessous, il faut placer des lamelles de contact sur les roues. Vous
vous souvenez certainement que j'avais pris soin de monter des roues
isolées des 2 cotés ? C'était pour ça, et aussi pour éviter de voir le châssis relié aux rails !
Je colle donc, à la cyano, deux petites chutes de circuit imprimé sous
la traverse du bogie, je mets en forme une lamelle en chrysocale, et je
soude.

N'ayant pas de gabarit de pliage, la forme des lamelles n'est pas très régulière d'une roue à l'autre.
Après c'est simple... "le fil rouge sur les roues de droite et le fil noir sur les roues de gauche". Ou l'inverse, c'est comme vous voulez !

Notez, sur cette photo, que j'ai réussi à changer les attelages. Je vais pouvoir transférer les boitiers NEM si nécessaire.
Notez aussi la quantité de LEST ajoutée dans l'épaisseur du châssis, pour rendre l'ensemble plus stable (plombs de pèche).
J'ai maintenant le courant dans la cabine ! cool !
5/ La pièce prototypée... pas si simple !
J'ai bien étudié une première solution qui utilisait des tôles en
laiton pliées. Mais les formes doivent être TRES précises, ce qui risque d'être difficile à
cause des pliages approximatifs et des tolérances très réduites. Et
quand on fait le compte des fonctions à assurer (fixations,
guidages,...) et des soudures à faire, on abandonne assez vite cette
idée.


Cette solution m'obligeait aussi à
souder le tube de 4mm (en vert foncé ci-dessus) sur le plancher pour guider l'axe de rotation de la
cabine autour de la vis M2. Donc PAS GLOP !, Solution abandonnée.
Il existe une seconde possibilité en réalisant une pièce
prototypée (en vert clair) qui englobe l'ensemble des composants et assure la majorité des fonctions. Le dessin ci-dessous
montre aussi la carte électronique (en rose) située directement contre
la face arrière des moteurs
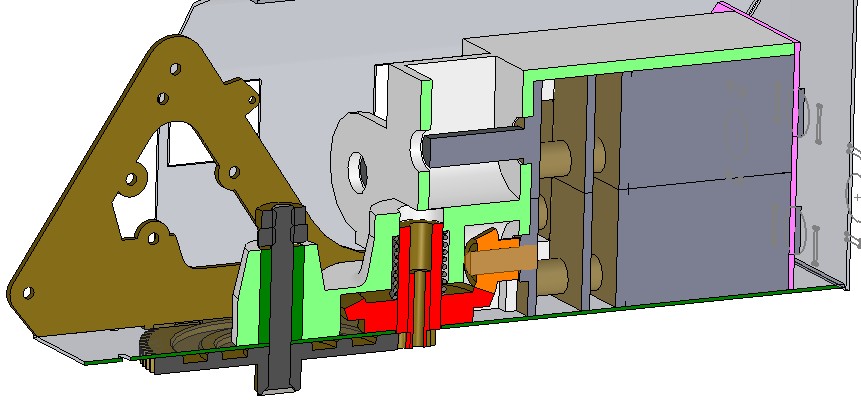
Lorsqu'on pense avoir fait le tour des fonctions, on peut lancer l'impression 3D.
J'ai utilisé plusieurs procédés d'impression avec un taux de réussite très variable :

- Les deux de gauche (gris et rouge) sont fabriqués en PLA sur une
machine "Réplicator". Cette machine utilise le procédé d'impression FDM
(Fused Deposition Modeling).
Le résultat n'est pas DU TOUT à la hauteur. Les trous sont ovales et
les dimensions ne sont pas respectées. Bref, inutilisables ! 
- Les trois autres de droite utilisent le procédé SLS (Selective Laser
Sintering) qui consiste à étaler des couches de poudre en ne fixant que
les endroits souhaités. Le résultat est bien meilleur. La dernière
pièce à droite est la dernière version en date...
J'ai prévu quelques sur-épaisseurs d'usinage dans le modèle afin d'ajuster
chaque trou au diamètre EXACT souhaité. Je peux ainsi rentrer les
différents éléments en place en accordant ou non un jeu radial.

La pièce ci-dessus n'est pas la version définitive. Elle n'était pas
assez solide et elle comportait quelques erreurs de dimensions. Et dans cette version, les poulies n'étaient pas guidées.
Celle-ci est déjà plus proche de la version finale. J'y ai ajouté deux
écrous pour le maintien sur la plaque et le perçage pour l'appui sur
les cordes à piano.

Si vous voulez télécharger le plan de la pièce ou même carrément le modèle 3D, cliquez sur les images ci-dessous :
Le plan en pdf |
modèle 3D au format STEP |
fichier STL pour impression 3D
|
 |

|

|
Voici la version du 24/04/2016, en place pour le premier essai de la rotation..... Ça marche !!!!

Sous 6Volts, ça tourne tout doux, exactement comme dans mes rêves !
6/ Les 3 autres mouvements (2 crochets et la flèche)
6-a/ Trois moteurs...et c'est tout !
Ils sont bien moins compliqués à mettre en œuvre (ou presque !). Ils
n'ont besoin que d'un axe tournant pour enrouler le fil. C'est chose
faite avec les longs axes des moteurs. Il faut seulement ajouter
une poulie au-dessus, par mouvement, afin de guider proprement chaque câble
jusqu'au tambour voulu.
- Le tambour central sert à monter ou descendre la flèche
- Le tambour de gauche sert à monter/descendre le crochet principal
- Le tambour de droite sert à monter/descendre le crochet secondaire
Les moteurs choisis ont une vitesse relativement élevée (180 tours par
minute sous 6 volts). De toute façon, la vitesse est réglée au
potentiomètre de la centrale. Donc pas de souci de ce coté.
6-b/ Les câbles... Pas simple du tout !!!!
Pour les câbles, j'avais pensé à prendre du fil de nylon monobrin de
0.26mm mais ce dernier était beaucoup trop rigide. Il ne s'enroulait
pas naturellement autour des poulies. La tension nécessaire pour
l'enrouler convenablement n'était pas raisonnable. J'ai donc effectué
un test avec plusieurs fils. Sur l'image ci-dessous, j'ai comparé le
comportement des fils avec la même masse suspendue. Il s'avère que le
fil de 0.1mm
de diamètre a le meilleur comportement. Mais 0.1mm ! Il est quasi
invisible ! C'est pas le but !

J'ai aussi testé les fils de couture en coton et en polyester. Le
résultat est très bon pour le rayon d'enroulement mais ils ont une
fâcheuse tendance à s'entortiller naturellement. Et ça ce n'est pas bon
pour lutter contre les sacs de nœuds.
6-c/ Les crochets :
Le
détail le plus problématique concerne donc la tension des brins.
L'utilisation d'un lest sur chaque crochet était donc indispensable
pour 2 raisons :
1- Pour éviter que les fils ne pendouillent mollement lorsqu'ils ne sont pas tendus, car C'EST PAS BEAU !
2- Pour que le fil reste guidé au fond de la gorge des poulies. La tension perpétuelle est indispensable.
Il n'y a que l'ajout d'un lest au bout du fil qui puisse assurer ces deux
impératifs. Je ne pense pas nécessaire de lester la flèche compte tenu
de l'angle de traction des 12 brins. En revanche, les crochets fournis avec le kit sont BEAUCOUP TROP légers
!!!! La
preuve c'est que la photo sur la boite du kit montre une grue avec les
fils qui se "tordent de rire" d'un bout à l'autre. J'ai donc viré les
pièces fournies pour réaliser intégralement un crochet en plomb.

J'ai volontairement choisi de former un crochet légèrement surdimensionné
de façon à l'alourdir le plus possible.
J'ai patiemment creusé le crochet pour contenir exactement les deux
poulies à l'intérieur. Malgré tout, j'arrive difficilement à obtenir un
crochet de plus de 5 grammes. c'est limite mais c'est déjà mieux que les 0,2
grammes des pièces originales. Il faudra
ajouter des composants pour plomber tout ça...
Avec cette masse, le comportement des fils est un peu meilleur :

Là encore, le 0.1mm est le meilleur mais son invisibilité est problématique. J'ai finalement choisi du fil de pèche tressé de 0.16mm de diamètre (décathlon, rayon pêche).
Au moment du montage, le problème essentiel consiste surtout à enrouler
le fil sur le bon moteur, dans le bon sens, en passant dans les bonnes poulies. C'est assez simple finalement.
7/ Digitalisation :
Bah oui ! Si je souhaite contrôler chaque mouvement
individuellement, il faut digitaliser ! La question du placement des
éléments a été résolue dès le départ. Ça ne devrait pas être un
problème.
La face arrière des moteurs se prête bigrement bien à cette fonction.
Elle permet en même temps de maintenir les moteurs et faire les
connections. Le décodeur
peut être mis en place au-dessus à l'aide d'un connecteur à 21 broches..
Voyons d'abord le schéma de câblage :

Ce sont les fonctions AUX1 et AUX2 qui vont contrôler les 4 moteurs en réalisant une combinaison des deux sorties.
Un mappage sera nécessaire au niveau du décodeur.
Fonction de commande (centrale)
| sortie AUX1
| Sortie AUX2
| Moteur contrôlé
|
Aucune ou F1 seule
| 0
| 0
| Montée-Descente flèche |
F2 . /F3. /F4
| 1
| 0
| Crochet principal
|
F3. /F4
| 0
| 0
| Crochet secondaire |
F4
| 1
| 1
| Rotation cabine |
Remarque : le symbole "/Fx" signifie que la
fonction "x" ne doit pas être sélectionnée. Ainsi, la mise en action
d'une fonction désactive toutes celles "inférieures". Par exemple, la
mise en marche de la fonction F4 active la rotation de la chaine et
désactive les autres mouvements.
Je m'empresse de réaliser un circuit imprimé adapté à la situation. Un véritable Gruyère !
- Les 4 gros trous servent à centrer l'arrière des moteurs
- Les 4 petits trous servent à visser le C.I. contre la pièce prototypée
- Les 8 trous rectangulaires servent à passer les bornes des moteurs.
- Les 5 pastilles supérieures servent à relier le C.I. arrière avec le C.I. du dessus.

Sur la carte arrière (photo ci-dessus à gauche), seuls 2 relais (disponibles à cette adresse) et 2 straps sont mis en place.
Le circuit du dessus (photo ci-dessus à droite) reçoit un connecteur à 20 broches disponible à cette adresse.
On ne s'en rend pas compte mais la taille de l'ensemble est extrêmement petite. Le typon est téléchargeable ICI en pdf pour impression directe à l'échelle.
Lors de la fabrication de mon circuit, je me suis loupé sur l'insolation
,
et j'ai finalement réalisé le circuit à la main en prenant quand-même
le typon comme modèle pour positionner les perçages. Le résultat est
convenable malgré tout. J'ai fait de même pour le second circuit qui
sert de support au décodeur.

Notez
que j'ai rallongé le circuit du dessus afin d'agrandir la zone de
contact pour les palpeurs. Au final il mesure 24mm de long par 19mm de
large.
Le premier moteur à mettre en place (avant tout autre composant) est
celui du haut. Il faut replier les pattes du moteur au raz du circuit
(et même araser un peu à la Dremel) afin que les deux relais cms
plaquent correctement contre le cuivre. Ce moteur n'est plus démontable
ensuite (oui, je sais, c'est pas GLOP !)

Lorsque les 4 moteurs sont soudés, on peut mettre en place les 2
relais, les 2 straps et les 5 fils laiton de 0.5mm qui vont servir de
palpeurs de contact.

Globalement, l'encombrement est ARCHI-LIMITE ! Les deux relais
dépassent bien derrière et rentrent au micro-poil dans la cabine. OUF
!!!
Le maintien du circuit contre la pièce prototypée se fait à l'aide de 4
vis F-M2. Il faut percer la pièce prototypée au diamètre 1.8mm puis
rentrer les vis lentement pour former le taraudage. Il faut éviter de
serrer trop fort. Un simple maintien est largement suffisant. Les têtes des deux vis supérieures doivent être
réduites en diamètre (petit coup de lime) pour ne pas frotter
contre les relais.
Un petit test avec une alimentation 12v n'est pas superflu avant de fixer le décodeur. De mon coté, ça marche du premier coup.
Je connecte les palpeurs (DCC+ DCC-) avec la platine à l'aide de deux fils
émaillés, collés contre la paroi de la pièce prototypée. L'appui sur
les deux fils en laiton est indispensable pour optimiser l'effet
"ressort". Heureusement, j'ai prévu le trou pour la vis d'appui au
centre ! J'aurais-dû utiliser des cordes à piano de 0.3mm mais je n'en
n'avais pas sous la main...

J'ai rajouté deux pistes connectées à F0av et F0ar. Ces sorties, protégées ici par deux résistances de 1,2 kOhms, sont
réservées pour allumer les feux des locomotives. Je vais m'en servir
pour allumer des projecteurs situés sur la flèche.
Les projecteurs sont collés à la cristal clear puis recouverts de
peinture noire pour éviter les fuites de lumière par les cotés.

Ils sont TRES efficaces et TRES lumineux !
Leur présence me permet d'avoir une indication sur le sens du mouvement
sélectionné. à droite "ça monte", à gauche "ça descend". Evidemment, le
mode manœuvre permet d'allumer les deux projecteurs simultanément.
Il faut donc
amener 2 fils émaillés le long des poutrelles de la flèche et
prévoir une souplesse au niveau de l'articulation de la flèche. J'ai
donc fait le tour de l'axe d'articulation en formant un "S". L'ensemble
reste TRES discret.

Pour que le bloc de motorisation reste démontable, j'ai prévu une
connexion automatique par palpeurs à l'aide de fils en laiton de 0.5mm
et de chutes de circuit imprimé. Ça marche TRES bien !
8/ Montage final... Mise en place des fils.
L'assemblage final est assez aisé compte tenu de tous les éléments
concus précédemment. MAIS... la grosse difficulté consiste à placer les
fils dans les poulies dans faire une grosse pelote de noeuds. Un petit
jeu de patience !
D'abord, je monte définitivement les treuils à l'emplacement que je crois être le bon :

J'en profite pour noircir, salir, pâtiner l'ensemble "treuils".
J'ai pris soin d'enrouler une (une seule) couche de fil sur toute la
largeur des tambours afin de figurer un nombre important
d'enroulements. Ils sont collés à la cyano puis recouverts d'un mélange
de noir/rouille.
Je dévisse temporairement le bloc électrique pour reculer les moteurs
pendant la mise en place des fils autour des axes. Pratique !

Pour chaque mouvement il faut prévoir une quantité suffisante de fil.
- La flèche réclame la plus grande longueur avec environ 2 mètres de fil.
- Les deux autres n'ont besoin que d'environ 1m20.
Pour que l'enroulement se "déroule" (!!!) convenablement, il faut mettre en place des poulies de guidage au-dessus des moteurs.
Je
mets donc en place un axe en laiton de 1.5mm avec trois poulies. Les
deux poulies externes sont en biais pour guider les fils au bon
endroit. Le maintien des poulies se fait lors de la découpe de
l'excédent d'axe. L'écrasement provoqué par la pince forme un obstacle
bien suffisant pour empêcher le démontage de la poulie.

Malgré cela, je vais devoir ajouter des minuscules guides en fil laiton
de 0.2mm pour que le départ des fils se fasse à l'endroit optimal.
J'ai commencé par mettre en place les 12 brins de la flèche.
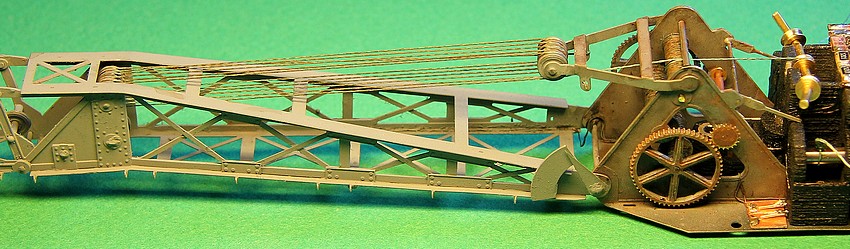
J'ai fait le tour du treuil supérieur afin qu'il tourne lors la levée
(ou descente) de la flèche. La couleur des câbles pourrait être plus
foncée.
Globalement, bien que la force de traction soit divisée par le nombre de brins, le câble est assez bien tendu et donne un assez bel effet.
J'ajoute un petit guide en fil laiton de 0.3mm pour amener le câble en face de la première poulie :

GROS PROBLEME : Bien que la montée se fasse sans souci (la force de
traction sur les fils est énorme !), la descente, en revanche est très
problématique. La seule force qui fait redescendre c'est le poids des
éléments, mais il est clairement insuffisant et les poulies coincent un
peu. L'ajout d'un peu d'huile est insuffisant, je vais revoir toutes les poulies pour leur enlever tout point dur. Pour l'instant,
c'est pas au top (voir la vidéo du 07/05/2016).
Le fil du crochet secondaire est bien plus facile à mettre en place.
J'utilise le second treuil. Le fonctionnement est bien meilleur car il
n'y a pas de mouflage et le nombre de poulies est
bien moindre. Une simple petite masse accrochée au bout assurera une descente
régulière. Là encore, je fais le tour du tambour intermédiaire afin que
la roue tourne pendant le mouvement. C'est du plus bel effet !

Le crochet principal possède aussi un mouflage, ce qui
divise la
tension des brins par 4 (et encore, j'ai triché j'aurais-dû faire 5
brins). Il faut ajouter une bonne grosse masse pour
garder l'ensemble bien tendu. Pendant le levage c'est nickel mais pour
la phase de descente j'ai dû ajouter un lest... 30 grammes !
Soyons fous !
Lorsque tous les fils sont en place et qu'on a testé le mouvement, on
peut fermer la cabine. Attention, seules les deux vis situées à
l'arrière de la cabine sont utilisables. Les deux autres ne peuvent
plus être placées car l'accès sous la cabine n'est pas possible.
Dernier point : J'envisage de laisser la cabine se déplacer en hauteur
afin de libérer le mouvement de rotation. Ainsi, elle pourra suivre son
wagon d'accompagnement dans les virages. Le système est à l'étude. Je vous tiens au courant...
9/ Mise en œuvre :
Bon, c'est bien joli tout ce bla-bla, mais comme moi, vous avez hâte de la voir fonctionner, non?
Bon, pour tout avouer, les premiers essais ne sont pas super
concluants. Je dois améliorer les mouvements de descente et le captage
du courant. Un bon rodage est rigoureusement nécessaire. A part ça,
c'est QUE DU BONHEUR !!!! J'y passerai des heures !

Il ne reste plus qu'à terminer la peinture, mettre les
vitrages et les marquages. Une petite patine générale ne fera pas de
mal.
Avec un projecteur allumé (gauche = on descend)

En mode manœuvre, les deux projecteurs sont allumés et les mouvements sont encore plus lents ! Génial !

Ouaip, c'est aveuglant !
Projecteur droit = On monte !

Allez, c'est parti pour la vidéo des premiers essais :
Le lien direct vers la vidéo est ici : Premiers essais de la grue CAILLARD motorisée
Et...oui,
je sais, il manque le VRAI wagon d'accompagnement.... Mais
rassurez-vous, c'est prévu pour le mois prochain ! Restez connectés !
J'ajouterai une vidéo dès qu'il sera prêt.
Et voilà ! C'est fini !
J'espère vous avoir donné envie de digitaliser votre grue. Et même si
vous ne la digitalisez pas, le kit est vraiment très sympa à réaliser.
Alors LANCEZ-VOUS !
Comme d'habitude, vous pouvez laisser vos commentaires bons ou mauvais (mais toujours constructifs) à mon adresse habituelle.
... La suite le mois prochain !...
10- Rail Expo 2016 :
Le 06 Novembre 2016, j'ai eu le plaisir de présenter cette grue sur le stand de SMD-Productions. La grue Caillard a vaillamment
fonctionné tout le samedi devant un grand nombre de personnes
intéressées.Merci à tous ceux qui m'ont fait part de leurs commentaires
encourageants.
La photo souvenir de cette folle journée sur le stand SMD-Productions :
Merci à Denis pour son accueil et sa générosité.
Bon... le soir on a eu un souci...
ça a marché jusqu'à ce que la centrale de commande nous fasse une
mauvaise blague... Le petit treuil s'est emballé pour une raison qui
nous échappe, et a provoqué une petite catastrophe dans les entrailles
de la bête. Rien de grave mais pendant la réparation, j'ai coupé d'un
fil électrique d'alimentation. Facile à réparer mais ça va demander
quelques minutes de travail. La grue ne sera donc pas visible le
Dimanche à Rail expo, ni Vendredi à Orléans.
Les réparations ont été vite faites. Pas de souci de ce coté. En
revanche, nous n'avons pas su utiliser la centrale TRIX le Samedi à
Orléans. Ok, j'ai honte !
Suite à cette présentation, et devant le succès évident, Denis MAGOT a
décidé de mettre au point un kit simple pour que chaque possesseur de la
grue puisse digitaliser à son tour sa ou ses grues. Le projet est à l'étude. Ca avance assez bien et les solutions sont vraiment propres ! Voyez sur le site de SMD pour les nouvelles.
En attendant, on bosse ! 