Barrière coulissante SMD
C'est l'un des kits les plus faciles que j'ai pu mettre en oeuvre
jusqu'à présent.
Vous allez voir, le montage est vraiment enfantin. En revanche, je n'ai
pas pu résister à la tentation de placer un moteur pour motoriser le
portail.
Dans cette page, vous trouverez tous les détails pour :
1/ Construction du kit :
Le kit se compose uniquement d'une plaque en arcap finement gravée :

On commence par empiler les deux lisses avec la barrière en se guidant
sur 5 tiges en laiton de 0.6mm (non fournies dans mon kit)

Attention à ne pas oublier les roues avant de poser la seconde lisse.
Et surtout, ne pas apporter trop de soudure pour que la roue puisse
tourner librement.

Pendant que ça refroidit, on peut s'attaquer au pliage des poteaux.
C'est une opération difficile car certains rebords à plier sont
vraiment très étroits. C'est le système D qui prévaut en absence
d'outillage adapté.

Le reste était tellement simple que j'ai apporté ma touche personnelle
: J'ai soudé deux vis M2 sous la base de chaque poteau afin de rendre
la fixation TRES solide ! Il faut que les vis soient strictement
perpendiculaires au support.

ATTENTION : les trous dans la planche doivent être bien verticaux
aussi, et
la distance qui les sépare ne doit SURTOUT PAS être inférieure à la
distance entre les deux vis. Sinon, le rail entre les poteaux va se
soulever en travers du chemin... c'est pas le but !
En prévoyant une distance de perçage légèrement plus écartée (un
micro-quart-de-poil en plus) le rail sera bien tendu entre les poteaux.
et la barrière coulissera bien à l'horizontale.

Les chapeaux sont assez simples à obtenir.
Il ne reste plus qu'à souder la rallonge du rail pour la position
ouverte. Cette pièce supplémentaire se trouve incluse dans la grappe du
kit. Il suffit de couper la longueur souhaitée !

Attention au bon allignement des deux rails !
Et voilà ! C'est fini pour l'assemblage de la barrière. Deux petites
heures auront suffit pour cette construction.
Reste à se pencher sur la suite : la motorisation !
2/ Motorisation et mise en place :
Evidemment, la motorisation se doit d'être invisible. Elle sera donc
sous la table.
Plusieurs solutions étaient possibles, sachant que le problème mejeur
consistait à transformer le mouvement de rotation (du moteur) en
translation (du portail) :
- Servomoteur avec
levier et bielle : C'était tentant...mais le débattement insuffisant et
les mouvements incontrôlés lors de la mise sous tension sont
problématiques.
- Moteur à rourant continu (ou pas-à-pas) avec courroie (genre
imprimante jet d'encre). Faisable, mais ça signifie que la courroie
apparaît au-dessus du plateau et les poulies ne sont pas facile à
cacher.
==> Il y a plus simple !
- Moteur à CC (ou pas-à-pas) avec pignon
et crémaillère. Tentant aussi, mais la
crémaillère coûte cher. L'avantage c'est que le guidage est réalisé
correctement. Donc c'est tentant mais je n'ai pas choici cette solution.
- Moteur à CC (ou pas-à-pas) avec vis
/ écrou. C'est pas cher, ça peut aller sous la table. Ca me
plait bien, je me lance !
En bon pédagogue que je suis, je me dois de montrer l'exemple que
j'inculque à mes étudiants, en commençant par un schéma cinématique :

La barrière est équipée d'un fil en laiton (en jaune ci-dessus) qui
traverse la planche. Le chariot (bleu) pousse la tige vers la droite ou
la gauche en fonction du sens de rotation de la vis. Le motoréducteur
est fixé contre le châssis. La tige filetée sera guidée à ses deux
extrémités.
Je découpe quelques chutes de circuit imprimé (époxy + cuivre) :
- 1 grand morceau de 160mm*20mm
- 4 morceaux de 11mm*20mm
- 4 équerres d'environ 11mm*11mm (peu importe la dimension horizontale,
seul l'angle droit est important).

Dans les 4 petits morceaux rectangulaires, je perce un trou de 4mm bien
au centre de chaque plaque. J'ai percé les 4 plaques en une fois pour
être sûr de la coaxialité.
Dans le petit rectangle de gauche, je vais fixer le moteur en utilisant
les vis qui tiennent le motoréducteur. Pour cela, il faut séparer le
réducteur en dévissant les deux vis :

(Pas de crainte de démontage du réducteur..il est serti !)
Le perçage de 4mm permet de centrer le réducteur. J'utilise donc ce
dernier comme gabarit pour perçer les deux trous diamétralement opposés
(en diagonale).
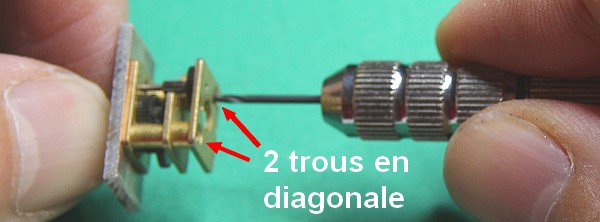
Sur la face restée libre, il faut percer (sans déboucher !) à
3.5mm pour que les têtes de vis puissent rentrer dans l'épaisseur de
l'époxy.
On peut ensuite souder cette petite plaque sur la grande plaque de
base. La perpendicularité sera obtenue à l'aide des deux équerres
découpées précédemment.

A l'autre bout de la grande plaque, on fait de même avec les deux
autres équerres et un autre petit rectangle percé.

Passons à la vis :
Le problème majeur consiste à relier la vis avec l'axe du moteur :
- L'axe du moteur fait 3mm de
diamètre avec un méplat.
- la vis mesure 4mm de diamètre
J'ai donc pris un tube en laiton de 4mm de diamètre (par 6mm de long).
J'ai limé l'extrémité de la vis TRES GROSSIEREMENT afin qu'elle rentre
en force dans le tube. La longueur insérée dans le tube est de 3mm. A
grands renforts de décapant, je noie cette liaison dans la soudure à
l'étain. Ca donne une liaison très solide.

ATTENTION à ce que le tube et la vis soient bien coaxiaux.
Si j'ai choisi un tube de 3mm (intérieur) c'est pas pour rien :
Il rentre pile-poil sur l'axe du moteur ! Le centrage est donc parfait.
En revanche, il fallait supprimer la rotation par rapport à l'arbre
moteur.... J'ai donc tout simplement écrasé le tube en laiton contre le
méplat du réducteur. C'est suffisant !

Concernant le coulisseau, le ne pouvais pas faire plus simple : J'ai
soudé un écrou entre les deux dernières plaques rectangulaires. Lors de
la soudure, j'ai placé l'ensemble sur la tige filetée, et serré avec
deux autres écrous pour un bon maintien.

J'ai quand-même pris soin d'araser la partie inférieure des plaques
afin de ne pas frotter trop fort contre la plaque de base.
Le tout se monte à la perfection. J'ajoute deux écrous (écrou +
contre-écrou) en guise de butée à l'autre extrémité de la vis, et le
tour est joué. On peut passer aux premiers essais.
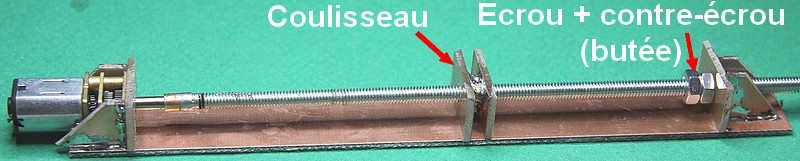
C'est pas mal, mais :
- il faut vraiment que l'axe du
moteur et la vis
soient coaxiaux ! Sinon ça provoque une petite variation de vitesse
assez déplaisante à chaque tour.
- le bruit du moteur est génant à partir de 6v
- la vitesse est trop lente à mon avis.
En attendant, ça marche. Et tout cela devra être placé sous la table...
Juste à la
verticale de la tige en laiton, je creuse une longue rainure. La
longueur minimale doit être en accord avec la course prévue.

Maintenant, on creuse un grand trou oblong dans la table à l'aide de la
dremel et de l'outil pour défoncer :

Pévoir un outil aussi fin que possible car la rainure doit rester
discrète du coté supérieur (visible). Elle sera en partie cachée sous
le rail.
Je soude la tige de laiton sur la barrière, du coté non visible par les
spaectateurs.

Avec ma maladresse
habituelle, j'ai réussi à tordre un barreau de la barrière :-((...
Ca parait rien comme ça..mais le passage entre les demi-poteaux
est très étroit... Donc à surveiller...
Je fais les branchements électriques avec deux butées de fin de course
selon le schéma ci-dessous :

- L'interrupteur inverseur permet
d'inverser la tension envoyée au moteur.
- Les contacts de fins de courses permettent d'interrompre le
courant quand la barrière doit s'arrêter.
- Les diodes 1N4007 sont parfaites pour cet usage.
Voici un aperçu du câblage sous la planche : Les couleurs des fils sont
conformes aux couleurs du schéma ci-dessus.

L'alimentation arrive sur les bornes externes de l'interrupteur
inverseur. Notez le sens de branchement des diodes en accord avec le
sens qu'elles contrôlent. Elles sont branchées sur la borne NF
(normalement fermée) du contact.
Je vérifie (sans la barrière) que le coulisseau se comporte comme
attendu aux deux bouts. Une fois réglé, je fixe définitivement les
contacts de fin de course.
Je recule le coulisseau en position ouverte pour mettre en place la
barrière. L'insertion se fait par dessus très facilement.
... et je bascule le levier....

Me voilà prêt à vous montrer la vidéo du
système : (n'ayez pas peur du
bruit... ce n'est qu'un petit moteur...)
Le lien direct vers la vidéo est ici : Motorisation
Barrière coulissante SMD
En
conclusion :
Pour un premier jet, je suis relativement content du résultat puisque
... ça marche !
Mais c'est encore perfectible... car je trouve le mouvement un peu trop lent et le bruit du moteur me déplait fortement.
Je vais donc poursuivre mes travaux pour améliorer le système avant la
mise en place de la barrière sur le réseau du club :

Voilà ! J'espère vous avoir donné envie de mettre cette barrière sur
votre réseau.
Et si cela vous inspire, n'hésitez pas à m'envoyer votre résultat à
l'adresse habituelle. Ca m'intéresse !